Research activities and projects
The Norwegian Tribology Center is a collaboration between SINTEF and NTNU through the Gemini Centre Tribology.
Our expertise covers different application areas such as Offshore, Railway, Hydropower, Process Industry, Surface Engineering and Coatings, modelling, etc.
Below are details from the current research activites and projects.
Maritime
Over 80% of the volume of international trade in goods is carried by sea. This implies that a large number of vessels are sailing all over the world. Use of lubricants in those vessels is critical for optimal performance of different equipment and moving parts, but in many cases the lubricants leak into the oceans. The environmental impact of lubricants in sea waters has trigger US EPA (United States Environmental Protection Agency) to launch the 2013 Vessel General Permit (VGP). The 2013 VGP establishes new rules forcing the use of environmentally acceptable lubricants (EAL) in all oil-to-sea interfaces unless technically infeasible. This regulation applies to all vessels bigger than 24 m operating within US Coastline.
In SINTEF and NTNU we closely work with international maritime companies, lubricant producers and subsuppliers to minimize the environmental impact by helping to replace hazardous and contaminant mineral oil by EALs (Environmentally Acceptable Lubricants).
More information about the project we work with are:
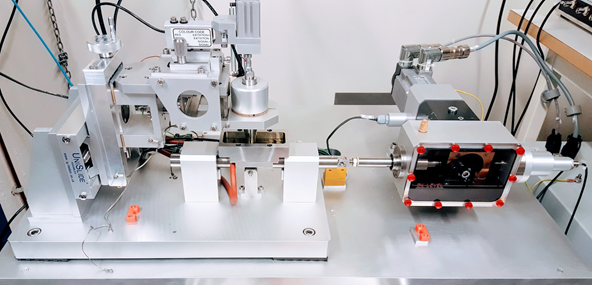
Railway
As rail transport usage continues to grow, maintaining the efficiency, sustainability, and safety of the system presents significant challenges. The railway lubrication process, an essential part of this system, currently faces key problems that need resolution. For instance, traditionally, the same lubrication system is used for both heavy and light rail operations. This one-size-fits-all approach often proves inefficient as the needs of heavy and light rail operations differ significantly. This disparity results in increased wear and tear, higher energy consumption, potential safety risks, and environmental pollution due to greenhouse gas emissions and metal debris release.
SINTEF, as a leading research organization, contributes significantly to several projects aiming to address these concerns. These projects focus on developing comprehensive lubrication systems that include innovative, environmentally friendly lubricants and advanced lubricant delivery systems tailored to the specific needs of both heavy and light rail operations. The ultimate goal is to enhance the efficiency, sustainability, and safety of Norwegian rail transportation.
Leveraging its expertise in material science, chemistry, mechanical engineering, and environmental sciences, SINTEF plays a pivotal role in these projects. The organization’s contributions range from the formulation of new lubricants and the design of delivery systems to the testing of these products under varying geographical and climatic conditions.
Emphasizing cooperative and interdisciplinary research, SINTEF ensures effective collaboration with various stakeholders in the railway sector. This approach ensures the developed solutions are practical, economically viable, and cater to the unique needs of different railway lines and systems.
SINTEF’s participation in such projects aligns with its mission to create a more sustainable and inclusive society. By improving the efficiency and sustainability of rail transportation, SINTEF contributes to reducing society’s carbon footprint and promoting cleaner, more environmentally friendly transport options. Furthermore, by helping to make rail travel safer and more reliable, SINTEF supports social inclusion, making travel easier and more affordable for a wider population.
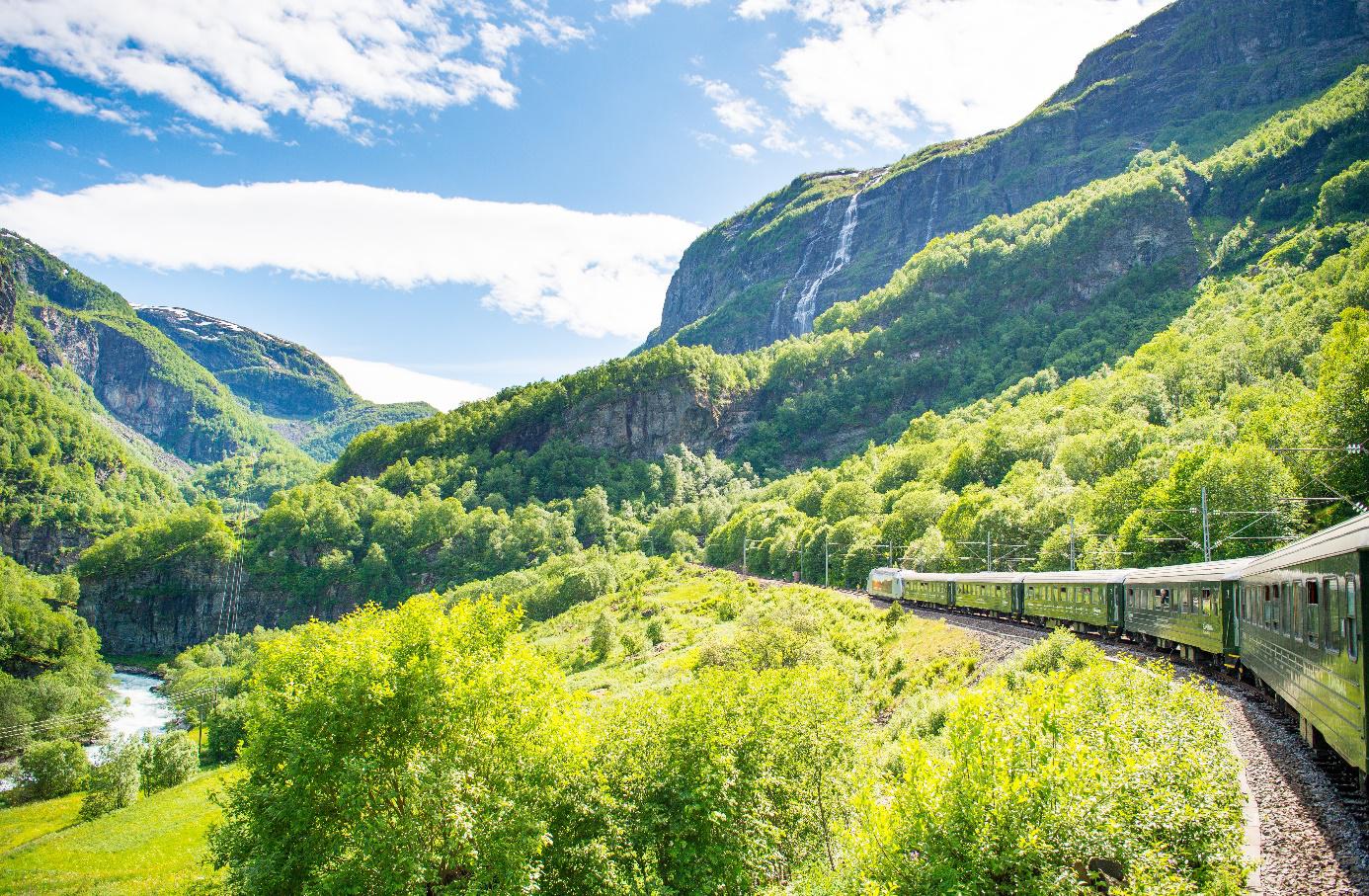
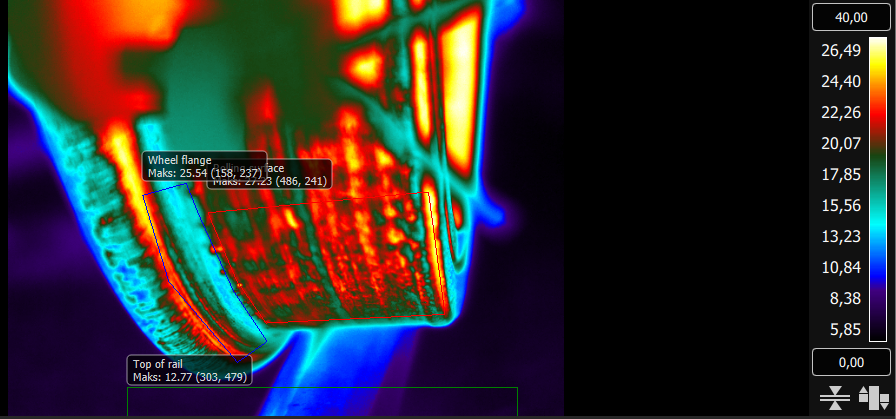
Formulating Environmentally Acceptable Lubricants by machine learning
Lubricant formulation and production is a century-old industry in which the development of formulations is still based on existing recipes adding selected additives. The new products need to be tested in a stepwise procedure, starting in lab scale and scaling up until real tests can be performed. This long, expensive, and often frustrating process can be boosted with the help of Machine Learning (ML). Formulating lubricants requires gathering information of available chemicals and substances that have the physical and chemical characteristics required for providing a system with the desired friction and wear. Learning from the available databases of chemicals that could potentially become the next generation of lubricants requires new tools, methods, and new approaches, radically different from those used until now. We are using a ML approach in which we are mining databases available online and experimental databases generated in-house to formulate new lubricants.
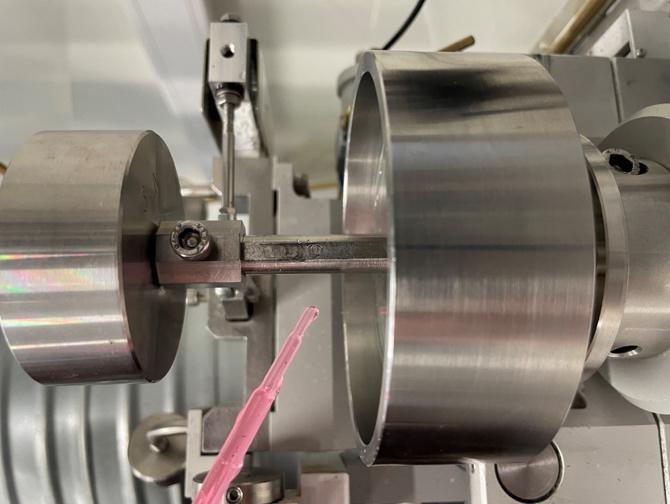
Metal Process Industri
Metal industry is one of Norway’s largest export industries. Production and forming of aluminum is the largest part of the Norwegian metal industry. One of the main challenges in production and forming of aluminum is that it tends to stick to surfaces during production and increase wear and degradation of most materials and coatings used in the forming tools. These mechanisms are complex tribological processes where a multidisciplinary approach (from tribological testing, materials physics, mechanics and structures and microstructures) is required to fully understand the degradation mechanisms. Advanced coating and lubricant technologies are constantly develop to minimize the wear, extend the lifetime of the forming tools, and enable new production processes of components with high-end quality. The Tribology Gemini Centre contributes to this development through different projects, such as:
https://www.sintef.no/en/projects/2017/galf-galling-in-aluminium-forming/
Link to CMS!
Norway also produces end-product metal components for different applications. Tailored properties of the final products can be achieved through new processing routines and heat treatment processes which the aim of maximizing the lifetime of the products. The tribology group is contributing to optimize the tribological properties of same alloys used in different products in different applications.
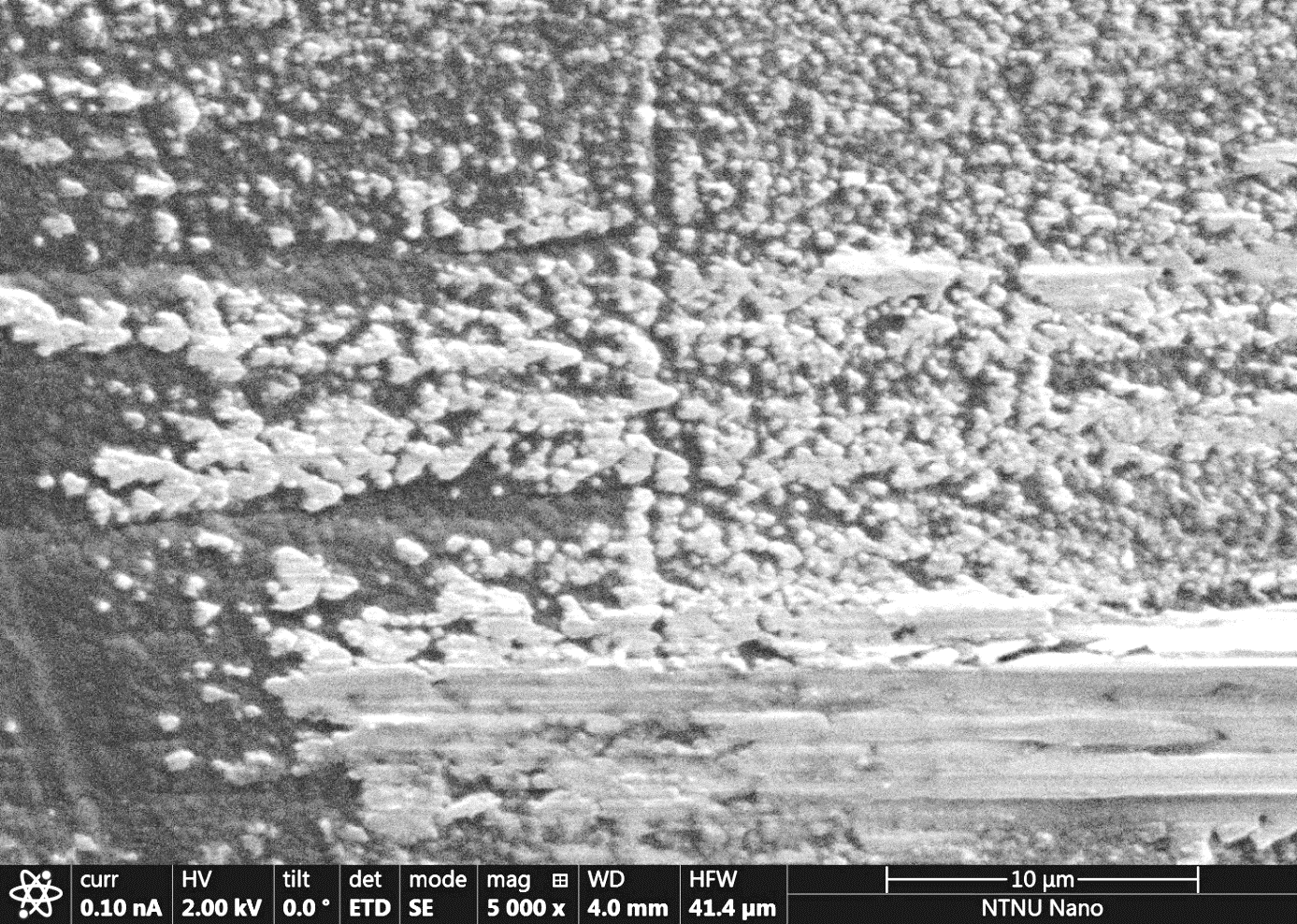
Offshore wind
Erosion on wind turbine leading edges reduces turbine performance and is one of the most critical degradation mechanisms (in terms of maintenance cost) occurring on wind turbine farms.
The Tribology Gemini Centre has developed a new modular test rig based on DNVGL-RP-0171 able to test and compare coatings and protective layers applied to the wind turbine blades in different working conditions.
https://www.sintef.no/en/projects/2017/coatlee-coatings-for-reduction-of-leading-edge-erosion/
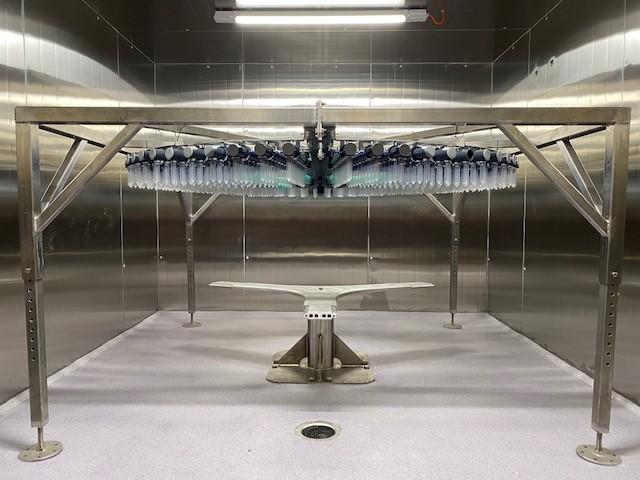
Oil and gas
Direct Riser Tensioner (DRT) cylinders are complex tribological systems which include the use of seals, guide bands, hydraulic fluids/lubricants and materials in relative movement. These components fail due to the combined effect of mult idegradation processes (friction, wear, corrosion and mechanical stresses). The origins of these degradation mechanisms lie at the atomic level and cause enormous economical loses, safety consequences and potential environment impact. Our research has contributed to better understanding the interaction of the elements of the tribological system at the atomistic level.
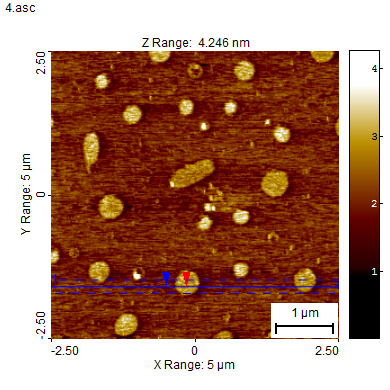
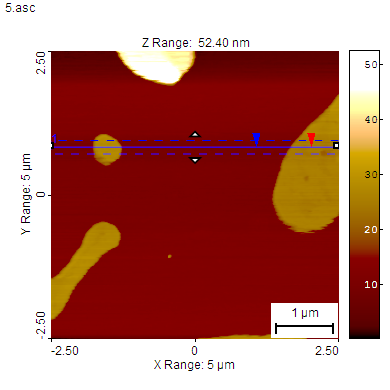
Modelling
Modelling superlubricity
Scaling Superlubricity into Persistence, SSLiP (EIC Pathfinder) on developing a way to utilise the atomic-level effect of structural superlubricity in macroscopic tribological systems.
Friction between moving parts and the associated wear are estimated to be directly responsible for 25% of the world’s energy consumption. SSLiP seeks to establish a radically new way to drastically reduce friction, with potentially enormous technological and societal impact. The driving concept is structural superlubricity, extremely low friction that takes place at a lattice misfit between clean, flat, rigid crystalline surfaces. Structural superlubricity is currently a lab curiosity limited to micrometer scale and laboratory times. SSLiP will bring this to the macroscale to impact real-life products. The key idea is the use of tribo-colloids: colloidal particles coated in 2D materials, that will produce a dynamic network of superlubric contacts. Structural incompatibility between arrays of colloids allows us to replicate the low friction on bigger length scales and overcome the statistical roughness of real surfaces. We will leverage our breakthrough result to regenerate the 2D coatings themselves during sliding. Through careful design of these coatings, carrier fluid, and the mechanical properties of the core particles, the chemistry of sliding and collective behaviour of the colloids can be controlled. Synthesis and experiments of individual contacts will be combined with visualisation of colloid dynamics during sliding on larger scales and in-site chemical characterisation. These will be combined with multiscale simulations and theory to bridge the different length scales into a coherent framework. The developed ultra-low friction technology will drastically reduce loss of energy, for example in passenger cars (responsible for around 2 billion tones of CO2 per year) and increase the lifetime of parts. It will also enable radically new technologies that are impossible with current lubrication, thus paving the way for e.g. much higher writing speeds in hard disks, where the writing tip will be able to move in full contact with the disk.
Nanotribology modelling
One of the main reasons why friction is such a challenging subject, is because many different effects occur at different scales. While two sliding surfaces appear flat on macroscopic scales, they are in fact almost never truly flat. On smaller scales, the roughness of the surfaces means that the actual contact area is small compared to the apparent contact area. The actual contacts are of the order of micrometer in size. Energy is dissipated in a variety of ways at these contacts by atomic interaction that occur on the scale of a nanometer. To understand friction on large, macroscopic scales, we must first understand friction on micro and nanometer scales. (The study of friction on very small scales is called nanotribology.) During the last few decades, there have been enormous developments in experimental techniques for probing friction on small scales, such as the atomic force microscope (AFM), but theoretical understanding is lagging behind. Theoretical techniques have also undergone developments: the mathematical understanding of dynamical systems as well as the massive increases in computing power have handed us the tools we need to finally understand friction. We study and model friction on this basic level. We employ detailed atomistic simulations as well, but our main focus here is on fundamental (qualitative, general) understanding and relatively simple models that contain the essential dynamics. We are for example interested in the behaviour of solid lubricants, molecules adsorbed on sliding surfaces, and structure of polymers.
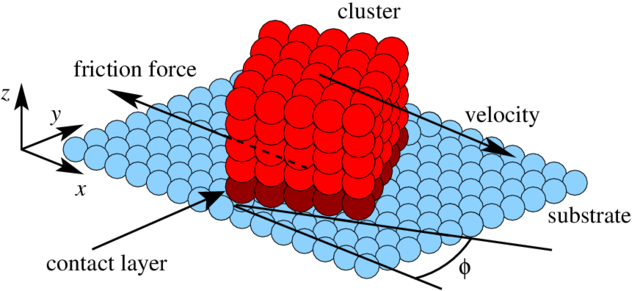

Superlubricity
Scaling Superlubricity into Persistence, SSLiP (EIC Pathfinder) on developing a way to utilise the atomic-level effect of structural superlubricity in macroscopic tribological systems.
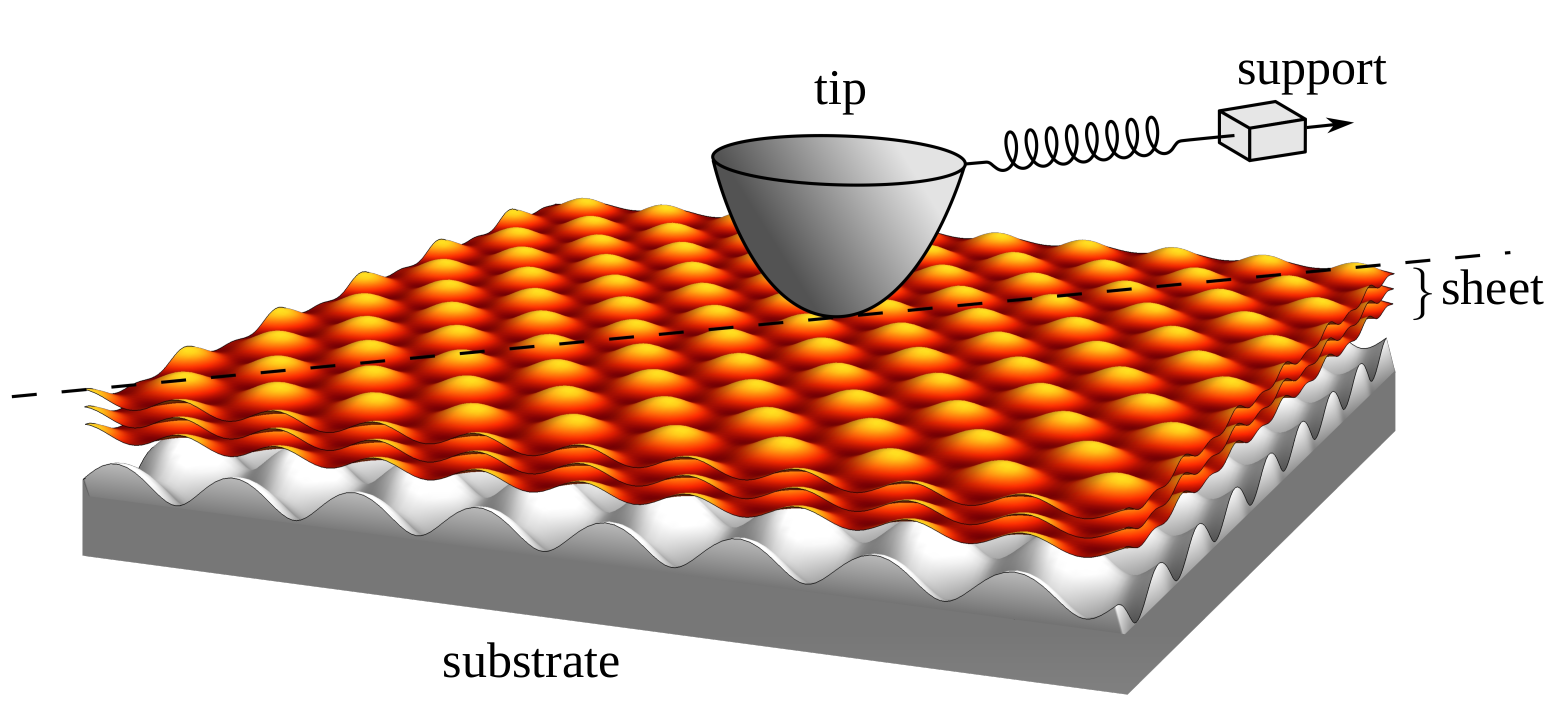
Structural superlubricity is currently a lab curiosity limited to micrometer scale and laboratory times. SSLiP will bring this to the macroscale to impact real-life products. The key idea is the use of tribo-colloids: colloidal particles coated in 2D materials, that will produce a dynamic network of superlubric contacts. Structural incompatibility between arrays of colloids allows us to replicate the low friction on bigger length scales and overcome the statistical roughness of real surfaces. We will leverage our breakthrough result to regenerate the 2D coatings themselves during sliding. Through careful design of these coatings, carrier fluid, and the mechanical properties of the core particles, the chemistry of sliding and collective behaviour of the colloids can be controlled. The SSLiP project includes experimental groups from Ireland, Germany, Italy, France, and the Netherlands, where synthesis and experiments of individual contacts will be combined with visualisation of colloid dynamics during sliding on larger scales and in-site chemical characterisation. These will be combined with modelling work at NTNU and Politecnico Milan, in the form multiscale simulations and theory to bridge the different length scales into a coherent framework. The developed ultra-low friction technology will drastically reduce loss of energy, for example in passenger cars (responsible for around 2 billion tones of CO2 per year) and increase the lifetime of parts. It will also enable radically new technologies that are impossible with current lubrication, thus paving the way for e.g. much higher writing speeds in hard disks, where the writing tip will be able to move in full contact with the disk.